Validation & Testing
WCM perform a series of solution-orientated test procedures on new and existing parts to ensure all requirements are met
To achieve full reliability and functionality of any given part, the team of engineering specialist at WCM employ a range of procedures to guarantee the solution conforms to its requirements. From supporting trial processes to test ‘fit for function’ exercises to working with experts from the wider team in Prototyping and Quality to assess fitment and dimensional data, WCM support projects right through to final manufacture.
Quality Testing Facilities
Quality facilities at WCM enable Engineering, Prototyping and Production teams to evaluate part tolerances and conditions with high accuracy, validating any design developments that take place.
- Large bridge CMMs for accurate part measurement up to 120 x 220 x 100cm
- 3D part scanning with direct CAD integration, enabling rapid progression during prototype stage
- Acoustic sound testing cell to carry out mechanical tolerance checks
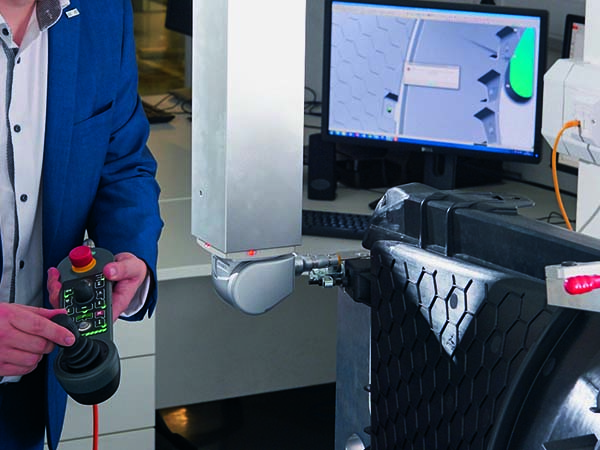
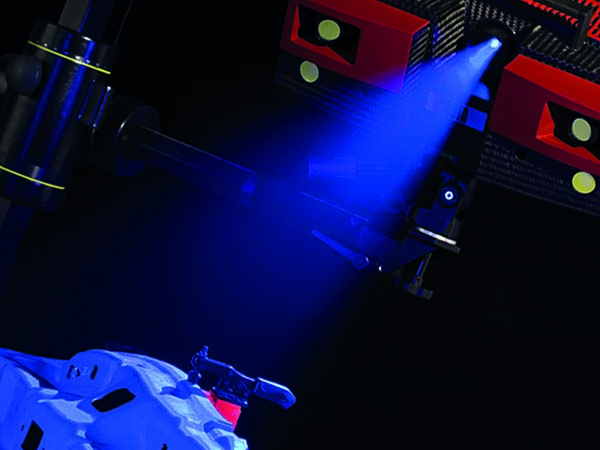
Engineering and Production Validation
Engineering and Quality operations support project teams across all phases of product development, assisting with early design development needs through to tooling requirements once the design stage has concluded.
- First-off Inspection Reports (FOIR)
- Initial Sample Inspection Reports (ISIR)
- Tool Trial Reports
- Batch Measurements (SPC)
- Casting Proofing/Mark Out/Machine to Cast
- Fault Finding by Measurement
- Reverse Engineering
- Multi-Cavity Inspection Reports
- Measurment System Analysis (MSA)
The validation and testing processes confirm that parts comply with all quality and performance targets